Roof Expansion & Contraction: How to Spot a Problem Before it Starts
If you live in the Northeast or another area of the U.S. that experiences the extremes of all four seasons, including hot summers and snowy winters, commercial roof expansion and contraction issues could become an issue for your facility. That’s because different temperatures and weather conditions can have a negative impact on all kinds of commercial building roof types. This includes metal, EPDM, single-ply, cool, foam, tar and gravel, rubber, PO, flat or shingle roofs.
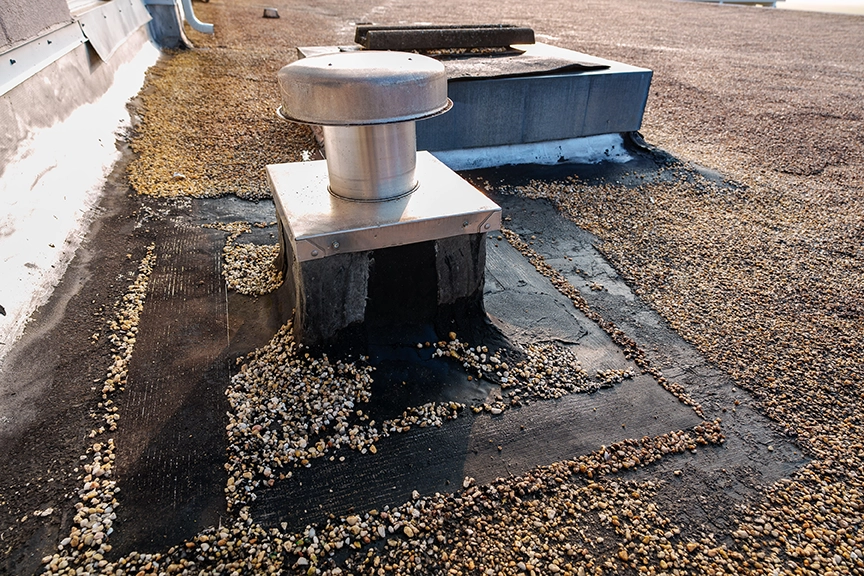
Roof expansion and contraction—also known as “thermal movement”—is not easily seen at first. The degree of changes over a short period of time can be small, but the constant movement over repeated seasonal cycles of temperature fluctuations can cause significant damage. Depending on the material, metal commercial roofs have been shown to exhibit expansion and contraction of nearly 1.25 inches over a 40-foot section.
To prevent a potential emergency roof repair cost, facility managers should be aware of the four most common conditions related to roof expansion and contraction issues. By becoming knowledgeable about shrinkage, moisture, temperature, and weather issues, facility managers can ensure they have the correct type of commercial roof for the climate in which their facility resides, and it’s properly protected.
Shrinkage
Although most commercial roof types are extremely durable and long-lasting, these benefits come with a significant tradeoff if the roofing material expands with the summer heat and contracts when temperatures dip below freezing. As a result, facility managers may notice that certain components of the roof—everything from the flashing to drip edges—can change in size over time. This frequent expansion and contraction can cause long-term structural issues that may need to be addressed to preserve the integrity of the roof and all of its components.
Moisture
The presence of moisture in the spring and summer months combined with heat results in humidity. This issue is very prevalent in the southern U.S. As a result of these conditions, mold and mildew can form and multiply, damaging the roofing material and diminishing the strength of the roof’s components, such as the joists, rafters, and the sheathing or decking. By addressing moisture issues, facility managers will prevent health and safety risks while also minimizing the potential chance of structural damage and costly repairs needed for the roofing system.
Temperature
Temperatures in the desert southwest of the U.S. can reach well over 100 degrees daily during the summer months. Regular, extreme heat can directly impact a roof’s vulnerable components resulting in damage. Heat rising from the interior of a commercial facility can cause the roof to develop weak spots, cracks, and leaks, and the extreme temperatures on the exterior of a roof can also result in the roofing material curling and shrinking. Roof membranes are designed to withstand a certain amount of temperature fluctuation; however, extreme or prolonged exposure to heat can weaken commercial roof materials and make them more prone to cracking or leaking.
On the other end of the spectrum, frigid temperatures can create damage to a commercial roof when the roofing material contracts. Contraction can cause commercial roof membranes or components to crack or pull away from one other, creating gaps where water can enter producing leaks or other damage.
Weather
Weather can also have a direct impact on a commercial roof system. Rain and snow can cause water to accumulate on the roofing material, making it more susceptible to damage from leaks or corrosion. In colder climates, inadequate drainage can contribute to the formation of ice dams, which occur when a roof contracts and the melted snow re-freezes near the roof’s edge, forming a barrier that prevents proper drainage. This trapped water can seep into the roofing system, causing leaks and water damage, while also compromising the building’s insulation.
To prevent commercial roof expansion and contraction issues from occurring, facility managers should ensure all components of their commercial roof are inspected and maintained regularly by a qualified roofing professional. A licensed and insured roofing professional will ensure you are using the right roofing material, it is being employed correctly, and will help identify and address any expansion and contraction issues. Contact us to set up an industrial roof assessment, or to talk about a commercial roof maintenance program to confirm your commercial roof is functioning properly.